Hummingbird MES and hyperMILL® CAD/CAM solution ensure efficient processes
Successfully implementing digital process control and optimization in production with an integrated CAD/CAM/MES solution
These days, everyone in manufacturing is talking about Industry 4.0 or intelligent, digitalized and transparent production. A key tool in this context is a Manufacturing Execution System (MES), which is essentially a control and planning system for production. So, what exactly is a MES?
Marcus Kalbacher: Of course, there is a proper definition for a MES. However, not all MES’ are the same. This means that no two customers have the same MES. Let me illustrate what a MES is like this. Even though the employees are giving 100%, the machines are not operating at capacity or throughput times are too long. Why is that? There are too many unproductive activities in the business. A MES takes care of these issues, thus ensuring properly organized, secure, and process-automated value creation.
Does a MES only make sense for certain industries sectors and/or companies of a particular size?
Marcus Kalbacher: The answer to this question is a clear no. In principle, the use of a MES makes sense across all industries and for companies of any size. Our agile Hummingbird MES is suitable for every industry and any company size. For efficient production, it is important that all relevant data can be called up and viewed in real-time. A production manager needs to know what is currently happening on the machines and where the various tools are being used. A manager also needs to know what NC program is available and at which location, or the current status of the milling or turning operation. It is even more important to know what processes are not running smoothly. For example, where is production not going as expected, and where are components missing? Employees should not waste valuable time gathering or looking for information. This is the only way to properly control and optimize processes. All necessary information must therefore be available online and automatically. In principle, this applies not only to production, but also to engineering, design, programming, quality assurance and much more.
Process control and optimization are important aspects of production. Is a major solution always needed here?
Marcus Kalbacher: Again, my answer is a clear no. Hummingbird MES has a modular structure, which makes the tool very flexible. This allows us to efficiently support small and medium-sized companies. Every project is unique. A company with three employees has different requirements than a large company. We support all customers and assist in all project stages to identify the best solution together. This can be an individual entry-level package, which can be put into operation in a very short time and without a consulting budget, all the way to a long-term solution. Successful project support always means adapting to the individual evolution of each company. We aim to offer our customers the right solution for their needs. Hummingbird MES grows with the changing requirements of the customer. Small companies and their challenges are just as important to us as large businesses.
Give us a few examples from the industry? What are the application scenarios for Hummingbird MES and the CAD/CAM solution hyperMILL® in a company?
Marcus Kalbacher: The CAD/CAM system like our hyperMILL® solution is a crucial component for connected manufacturing and a key source of data. It is therefore extremely important that data reliably reaches the respective workstation. There are many examples. The following quote from Krisztina Zwick, Managing Director of our customer Euroform Kft, sums it up nicely: “If you buy an automated machine for 24-hour production, you’ll achieve more throughput with the same number of staff. But it’s not that easy in day-to-day business, given all the complexity and dynamics.”
Efficient production also requires that you organize your workflows accordingly, especially the communication between CAM and the machine. This customer used to save the NC programs from the CAM system in directories on the server and manually transferred them from the server to the controller one at a time. Now the digital NC program management of Hummingbird MES reliably transfers the NC data to the corresponding machine at the touch of a button. The MES also controls external NC program simulation for this and other customers. The process and data flow is fully automated. This automation in the background means that 100% of NC programs are now simulated – not just random samples as before. This makes production significantly safer, especially when dealing with an automation system.
In manufacturing, there are often existing business landscapes that comprise a wide variety of systems, such as an ERP system. Can you give us an example to illustrate the difference between the various solutions?
Marcus Kalbacher: Generally speaking, all systems are there for a reason, but each system has a specific focus. For example, ERP focuses on business organization and commercial processes, but not on production. A PDM/PLM system focuses on design data management. Automation cell management focuses on the control of the respective automation system, while a tool management system focuses on tool management.
Suppliers often try to deliver complete systems, but no system can be best-in-class across the board. Our agile Hummingbird MES connects systems for maximum efficiency. We offer our customers the freedom to select the systems that are truly necessary or suitable for their respective purposes and to use them together efficiently.
What specific benefits do you offer customers who want to use the CAD/CAM system hyperMILL® and Hummingbird MES?
Claudio Jorio: Seamless continuity while ensuring maximum flexibility. Our CAD/CAM system hyperMILL® and Hummingbird MES are two separate solutions, but this is not visible to the customer. Rather than providing a simple interface for data exchange that is prone to errors, we are talking about extremely deep system integration. The advantage of seamless integration is that we can take advantage of all the options delivered by both technologies in a single system, from planning through to machining. The synergies of both systems are combined. By concentrating on our strengths, we can create far-reaching developments that are continuously refined. Our customers benefit from this in the long term.
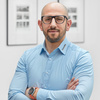